- ▶
- Heaters/Source
- ▶
- Agilent Heaters and SensorsMass Spectrometry, Scientific Supplies & ManufacturingScientific Instrument Services 5973 Source Heater Tamper Resistant Allen Wrench 5973/5975 Quad Sensor 5985 Source Heater Assembly Agilent Interface Heater Assembly 5971 Interface Heater
- ▶
- LiteratureApplication Notes Adsorbent Resins Guide Mass Spec Tips SDS Sheets FAQ MS Calibration Compound Spectra Manuals MS Links/Labs/ Organizations MS Online Tools Flyers on Products/Services Scientific Supplies Catalog About Us NextAdvance Bullet Blender® Homogenizer Protocols Micro-Mesh® Literature Instrumentation Literature Agilent GC/MS Literature SIS News / E-Mail Newsletter NIST MS Database - Update Notifications
- ▶
- Application NotesNote 103: EPA Method 325B, Novel Thermal Desorption Instrument Modification to Improve Sensitivity Note 102: Identification of Contaminants in Powdered Beverages by Direct Extraction Thermal Desorption GC/MS Note 101: Identification of Contaminants in Powdered Foods by Direct Extraction Thermal Desorption GC/MS Note 100: Volatile and Semi-Volatile Profile Comparison of Whole Versus Cracked Versus Dry Homogenized Barley Grains by Direct Thermal Extraction Note 99: Volatile and Semi-Volatile Profile Comparison of Whole vs. Dry Homogenized Wheat, Rye and Barley Grains by Direct Thermal Extraction GC/MS Note 98: Flavor and Aroma Profiles of Truffle Oils by Thermal Desorption GC/MS Note 97: Flavor Profiles of Imported and Domestic Beers by Purge & Trap Thermal Desorption GC/MS Note 96: Reducing Warping in Mass Spectrometer Filaments, with SISAlloy® Yttria/Rhenium Filaments Note 95: Detection of Explosives on Clothing Material by Direct and AirSampling Thermal Desorption GC/MS Note 94: Detection of Nepetalactone in the Nepeta Cataria Plant by Thermal Desorption GC/MS Note 93: Detection of Benzene in Carbonated Beverages with Purge & Trap Thermal Desorption GC/MS Note 92: Yttria Coated Mass Spectrometer Filaments Note 91: AutoProbe DEP Probe Tip Temperatures Note 90: An Automated MS Direct Probe for use in an Open Access Environment Note 89: Quantitation of Organics via a Mass Spectrometer Automated Direct Probe Note 88: Analysis of Silicone Contaminants on Electronic Components by Thermal Desorption GC-MS Note 87: Design and Development of an Automated Direct Probe for a Mass Spectrometer Note 86: Simulation of a Unique Cylindrical Quadrupole Mass Analyzer Using SIMION 7.0. Note 85: Replacing an Electron Multiplier in the Agilent (HP) 5973 MSD Note 84: Vacuum Pump Exhaust Filters - Charcoal Exhaust Traps Note 83: Vacuum Pump Exhaust Filters - Oil Mist Eliminators Note 82: Vacuum Pump Exhaust Filters Note 81: Rapid Bacterial Chemotaxonomy By DirectProbe/MSD Note 80: Design, Development and Testing of a Microprocessor ControlledAutomated Short Path Thermal Desorption Apparatus Note 79: Volatile Organic Compounds From Electron Beam Cured and Partially Electron Beam Cured Packaging Using Automated Short Path Thermal Desorption Note 78: A New Solution to Eliminate MS Down-Time With No-Tool-Changing of Analytical GC Columns Note 77: The Determination of Volatile Organic Compounds in VacuumSystem Components Note 76: Determination of the Sensitivity of a CRIMS System Note 75: An Apparatus for Sampling Volatile Organics From LivePlant Material Using Short Path Thermal Desorption Note 74: Examination of Source Design in Electrospray-TOF Using SIMION 3D Note 73: The Analysis of Perfumes and their Effect on Indoor Air Pollution Note 72: 1998 Version of the NIST/EPA/NIH Mass Spectral Library, NIST98 Note 71: Flavor Profile Determination of Rice Samples Using Shor tPath Thermal Desorption GC Methods Note 70: Application of SIMION 6.0 To a Study of the Finkelstein Ion Source: Part II Note 69: Application of SIMION 6.0 To a Study of the Finkelstein Ion Source: Part 1 Note 68: Use of a PC Plug-In UV-Vis Spectrometer To Monitor the Plasma Conditions In GC-CRIMS Note 67: Using Chemical Reaction Interface Mass Spectrometry (CRIMS) To Monitor Bacterial Transport In In Situ Bioremediation Note 66: Probe Tip Design For the Optimization of Direct Insertion Probe Performance Note 65: Determination of Ethylene by Adsorbent Trapping and Thermal Desorption - Gas Chromatography Note 64: Comparison of Various GC/MS Techniques For the Analysis of Black Pepper (Piper Nigrum) Note 63: Determination of Volatile and Semi-Volatile Organics in Printer Toners Using Thermal Desorption GC Techniques Note 62: Analysis of Polymer Samples Using a Direct Insertion Probe and EI Ionization Note 61: Analysis of Sugars Via a New DEP Probe Tip For Use With theDirect Probe On the HP5973 MSD Note 60: Programmable Temperature Ramping of Samples Analyzed ViaDirect Thermal Extraction GC/MS Note 59: Computer Modeling of a TOF Reflectron With Gridless Reflector Using SIMION 3D Note 58: Direct Probe Analysis and Identification of Multicomponent Pharmaceutical Samples via Electron Impact MS Note 57: Aroma Profiles of Lavandula species Note 56: Mass Spec Maintenance & Cleaning Utilizing Micro-Mesh® Abrasive Sheets Note 55: Seasonal Variation in Flower Volatiles Note 54: Identification of Volatile Organic Compounds in Office Products Note 53: SIMION 3D v6.0 Ion Optics Simulation Software Note 52: Computer Modeling of Ion Optics in Time-of-Flight mass Spectrometry Using SIMION 3D Note 51: Development and Characterization of a New Chemical Reaction Interface for the Detection of Nonradioisotopically Labeled Analytes Using Mass Spectrometry (CRIMS) Note 50: The Analysis of Multiple Component Drug Samples Using a Direct Probe Interfaced to the HP 5973 MSD Note 49: Analysis of Cocaine Utilizing a New Direct Insertion Probe on a Hewlett Packard 5973 MSD Note 48: Demonstration of Sensitivity Levels For the Detection of Caffeine Using a New Direct Probe and Inlet for the HP 5973 MSD Note 47: The Application Of SIMION 6.0 To Problems In Time-of-Flight Mass Spectrometry Note 46: Delayed Extraction and Laser Desorption: Time-lag Focusing and Beyond Note 45: Application of SIMION 6.0 to Filament Design for Mass Spectrometer Ionization Sources Note 44: The Design Of a New Direct Probe Inlet For a Mass Spectrometer Note 43: Volatile Organic Composition In Blueberries Note 42: The Influence of Pump Oil Purity on Roughing Pumps Note 41: Hydrocarbon Production in Pine by Direct Thermal Extraction Note 40: Comparison of Septa by Direct Thermal Extraction Note 39: Comparison of Sensitivity Of Headspace GC, Purge and Trap Thermal Desorption and Direct Thermal Extraction Techniques For Volatile Organics Note 38: A New Micro Cryo-Trap For Trapping Of Volatiles At the Front Of a GC Capillary Column Note 37: Volatile Organic Emissions from Automobile Tires Note 36: Identification Of Volatile Organic Compounds In a New Automobile Note 35: Volatile Organics Composition of Cranberries Note 34: Selection Of Thermal Desorption and Cryo-Trap Parameters In the Analysis Of Teas Note 33: Changes in Volatile Organic Composition in Milk Over Time Note 32: Selection and Use of Adsorbent Resins for Purge and Trap Thermal Desorption Applications Note 31: Volatile Organic Composition in Several Cultivars of Peaches Note 30: Comparison Of Cooking Oils By Direct Thermal Extraction and Purge and Trap GC/MS Note 29: Analysis Of Volatile Organics In Oil Base Paints By Automated Headspace Sampling and GC Cryo-Focusing Note 28: Analysis Of Volatile Organics In Latex Paints By Automated Headspace Sampling and GC Cryo-Focusing Note 27: Analysis of Volatile Organics In Soils By Automated Headspace GC Note 26: Volatile Organics Present in Recycled Air Aboard a Commercial Airliner Note 25: Flavor and Aroma in Natural Bee Honey Note 24: Selection of GC Guard Columns For Use With the GC Cryo-Trap Note 23: Frangrance Qualities in Colognes Note 22: Comparison Of Volatile Compounds In Latex Paints Note 21: Detection and Identification Of Volatile and Semi-Volatile Organics In Synthetic Polymers Used In Food and Pharmaceutical Packaging Note 20: Using Direct Thermal Desorption to Assess the Potential Pool of Styrene and 4-Phenylcyclohexene In Latex-Backed Carpets Note 19: A New Programmable Cryo-Cooling/Heating Trap for the Cryo-Focusing of Volatiles and Semi-Volatiles at the Head of GC Capillary Columns Note 18: Determination of Volatile Organic Compounds In Mushrooms Note 17: Identification of Volatile Organics in Wines Over Time Note 16: Analysis of Indoor Air and Sources of Indoor Air Contamination by Thermal Desorption Note 14: Identification of Volatiles and Semi-Volatiles In Carbonated Colas Note 13: Identification and Quantification of Semi-Volatiles In Soil Using Direct Thermal Desorption Note 12: Identification of the Volatile and Semi-Volatile Organics In Chewing Gums By Direct Thermal Desorption Note 11: Flavor/Fragrance Profiles of Instant and Ground Coffees By Short Path Thermal Desorption Note 10: Quantification of Naphthalene In a Contaminated Pharmaceutical Product By Short Path Thermal Desorption Note 9: Methodologies For the Quantification Of Purge and Trap Thermal Desorption and Direct Thermal Desorption Analyses Note 8: Detection of Volatile Organic Compounds In Liquids Utilizing the Short Path Thermal Desorption System Note 7: Chemical Residue Analysis of Pharmaceuticals Using The Short Path Thermal Desorption System Note 6: Direct Thermal Analysis of Plastic Food Wraps Using the Short Path Thermal Desorption System Note 5: Direct Thermal Analysis Using the Short Path Thermal Desorption System Note 4: Direct Analysis of Spices and Coffee Note 3: Indoor Air Pollution Note 2: Detection of Arson Accelerants Using Dynamic Headspace with Tenax® Cartridges Thermal Desorption and Cryofocusing Note 1: Determination of Off-Odors and Other Volatile Organics In Food Packaging Films By Direct Thermal Analysis-GC-MS Tech No. "A" Note 14: Elimination of "Memory" Peaks in Thermal Desorption Improving Sensitivity in the H.P. 5971 MSD and Other Mass Spectrometers - Part I of II Improving Sensitivity in the H.P. 5971 MSD and Other Mass Spectrometers- Part II of II Adsorbent Resins Guide Development and Field Tests of an Automated Pyrolysis Insert for Gas Chromatography. Hydrocarbon Production in Pine by Direct Thermal Extraction A New Micro Cryo-Trap for the Trapping of Volatiles at the Front of a GC Capillary (019P) - Comparison of Septa by Direct Thermal Extraction Volatile Organic Composition in Blueberry Identification of Volatile Organic Compounds in Office Products Detection and Indentification of Volatiles in Oil Base Paintsby Headspace GC with On Column Cryo-Trapping Evaluation of Septa Using a Direct Thermal Extraction Technique INFLUENCE OF STORAGE ON BLUEBERRY VOLATILES Selection of Thermal Desorption and Cryo-Trap Parameters in the Analysis of Teas Redesign and Performance of a Diffusion Based Solvent Removal Interface for LC/MS The Design of a New Direct Probe Inlet for a Mass Spectrometer Analytes Using Mass Spectrometry (CRIMS) Application of SIMION 6.0 to Filament Design for Mass Spectrometer Ionization Sources A Student Guide for SIMION Modeling Software Application of SIMION 6.0 to Problems in Time-of-flight Mass Spectrometry Comparison of Sensitivity of Headspace GC, Purge and TrapThermal Desorption and Direct Thermal Extraction Techniques forVolatile Organics The Influence of Pump Oil Purity on Roughing Pumps Analysis of Motor Oils Using Thermal Desorption-Gas Chromatography-Mass Spectrometry IDENTIFICATION OF VOLATILE ORGANIC COMPOUNDS IN PAPER PRODUCTS Computer Modeling of Ion Optics in Time-of-Flight mass Spectrometry using SIMION 3D Seasonal Variation in Flower Volatiles Development of and Automated Microprocessor Controlled Gas chromatograph Fraction Collector / Olfactometer Delayed Extraction and Laser Desorption: Time-lag Focusing and Beyond A New Micro Cryo-Trap for the Trapping of Volatiles at the Front of a GC Column Design of a Microprocessor Controlled Short Path Thermal Desorption Autosampler Computer Modeling of Ion Optics in Time-of-Flight Mass Spectrometry Using SIMION 3D Thermal Desorption Instrumentation for Characterization of Odors and Flavors
- ▶
- Improving Sensitivity in the H.P. 5971 MSD and Other Mass Spectrometers- Part II of II (This Page)
John J. Manura
Scientific Instrument Services, Ringoes, NJ
(Part I | Part II - Increasing Mass Spec Sensitivity)
Introduction
This article is the second of a two part series which describes the improvements and changes that we have incorporated into our HP 5971 MSD's in order to improve their sensitivity. In the last newsletter in Part I of this article we described improvements in the mass spectrometer or MSD component of the HP 5971 MSD System to improve its sensitivity (1). Part II of this article describes the improvements in the GC end of the system to achieve additional improvements in the baseline signal-to-noise ratios and therefore improvements in the sensitivity of the mass spectrometer. Although this discussion describes improvements made to the HP 5890 Series II GC and the HP 5971 MSD, the suggested changes and improvements described in this article can be applied to any GC/MS system in order to improve its sensitivity and performance.
In our attempts to improve the GC sensitivity, what we are trying to do is lower the background signal originating from the GC as well as improve the resolution of the GC peaks. Any signal or noise originating from the GC will contribute to baseline signal level and this in turn will restrict the level of analytes that can be detected by the mass spectrometer. There are many components of the GC which can contribute to the background. They can begin with the sample itself, the GC septum, the GC injection port, injection port liners and seals, the GC guard column and all the connecting lines. In addition the GC injection technique, the use of cryo-trapping and the selection of the type and size of the GC capillary column itself will also affect the ultimate sensitivity of the system. This article will describe each of these areas and discuss methods to eliminate or minimize background signal in the GC. In addition we will describe improvements that can be made to the GC system to maximize the signal-to-noise ratio for any analyte.
The following chart lists the major areas from which background signal can originate.
1. GC Injection Port
a. Septum
b. Injection Port Liners
c. Injection Port Liner Seals
d. Gas Transfer Lines
e. Syringe Needle
f. GC Column Inside Injection Port
g. Contaminated GC Injection Port
h. GC Carrier Gas
2. GC Oven
a. GC Guard Column
b. GC Capillary Column
c. GC Cryo-Trap
GC injection Port
Most of the contributions to GC background originate from the injection port of the GC. These problems originate both due to the design of the GC injection port as well as the parameters under which it is operated. The background originating from the GC injection port can be minimized by careful selection of the replacement parts such as the septa, liners and seals as well as the proper operating conditions such as operating temperature and septum purge. A typical GC injection port is shown in Figure # 1. This figure will be used to describe the various sources of GC background as well as ways to minimize the GC background.
Injection Port Design
The correct injection port temperature is important to assure complete sample volatilization and to eliminate contamination or 'memory effects' in subsequent GC injections. It is a common practice to set the GC injection port to about 50C higher in temperature than the temperature at which you will operate the capillary column inside the GC oven. This assures that no analytes will hang up in the injection port. However the entire injection port is not at the set temperature. One of the first things to note in Figure # 1 is the temperature gradient in the GC injection port. The injection port is set to 250C. However the temperature at the septum area is about 100 cooler in temperature than the set point. This has been purposely designed into the GC injection port by the manufacturer in order to minimize septum bleed. By keeping the septum at a lower temperature and using a septum purge, the bleed from the septum can be minimized. However these conditions also provide for the possible condensation of analytes on the underside of the septum or at the top of the injection port. These condensed analytes can either slowly bleed into the injection port during the GC run or they may be washed off the septum area with subsequent GC liquid injections.The GC carrier gas is not preheated in many GC's such as the HP 5890 series, unlike the Varian GC which preheats the carrier gas. This cool gas coming into the HP injection port contributes to the cooling effect at the septum area of the GC injection port and the resulting problems of septum area contamination. Preheating of the carrier gas can help eliminate some of these problems and we do indeed see less memory effects and septum contamination in the Varian GC in comparison to the HP GC. We have considered the manufacture of a column gas preheater for the HP injection port, however the cost of such a device would probably not be cost effective.
It is recommended that when injecting liquid samples into the GC injection port, that the syringe needle be injected fully into the GC injection port. This delivers the liquid sample to the bottom half of the injection port, far away from the GC septum. This minimizes the chance of the liquid sample and analytes from condensing in the septum area of the GC injection port. It also eliminates the possibility that the liquid solvent may wash off materials condensed on the septum from previous injections. However when liquid sample sizes greater than 1 ul are injected into the GC injection port, the rapid volume expansion that occurs in the phase transfer from liquid to gas forces the injected sample analytes into all areas of the GC injection port. Therefore keeping analytes from condensing on the septum is near impossible with conventional injection ports and injection port liners.
In thermal desorption and headspace injection techniques, gases are injected directly into the GC injection port through the GC septum. The gas sample being introduced into the GC injection port is usually quite hot. There is therefore the possibility that if the septum area is cool, the analytes in the sample will condense in the septum area of the injection port. If a syringe is used there is also the possibility that the sample might condense in the syringe needle itself. In one instance in which we were analyzing polynuclear aromatics with the thermal desorption technique, the higher boiling analytes condensed in the thermal desorption syringe needle even though the GC injection port was set to 325C. To overcome this condensation of semi-volatiles we developed a new low dead volume injection port liner to improve the heat transfer to the syringe needle and to the septum area of the injection port. This injection port liner is described below.
The selection of the temperature of the GC injection port can be perplexing. On one hand the higher the injection port temperature, the greater the degree of volatilization of the sample and the minimization of the amounts of analyte condensed in the septum area. However lower injection port temperatures result in less septum bleed, less sample decomposition and less column bleed from the GC column inside the bottom of the GC injection port. We typically set the injection port temperature to between 0 and 25 degrees above the maximum temperature that the GC column will be programmed to inside the GC oven.
GC Septum
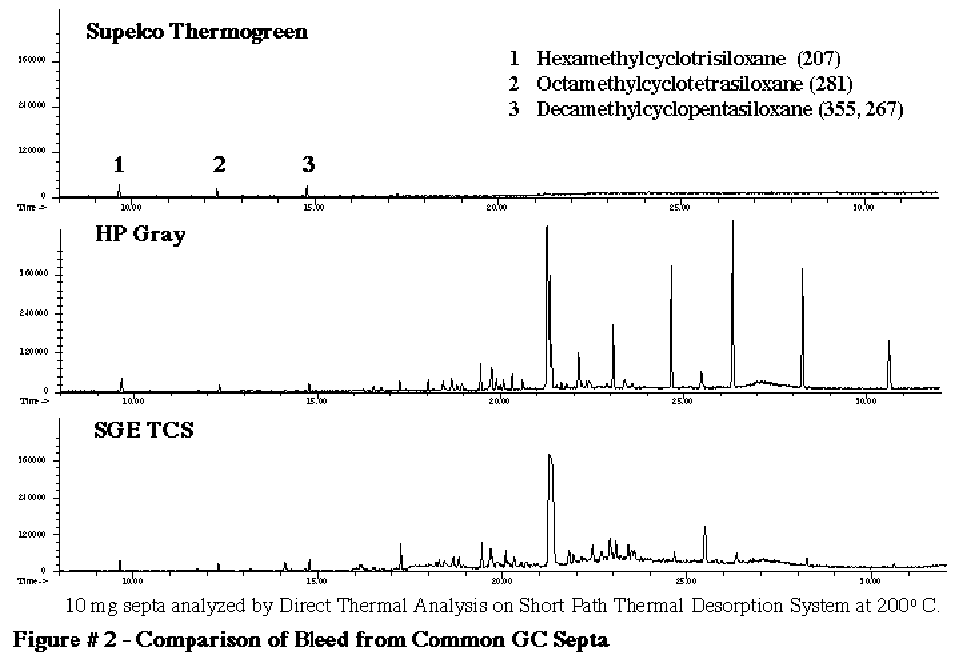
The most common source of GC background is the GC septum. Most GC septum are constructed of silicone. The common mass spec background peaks appearing at mass values of 207, 281, 267 and 355 can all originate from the siloxanes in the GC septa. In order to study this further we performed a series of studies to determine the degrees of background contamination that can originate from the GC septum from different manufacturers. We utilized our Short Path Thermal Desorption System in the direct thermal extraction mode. Ten (10.0) milligrams of each of the septum was placed inside the thermal desorption tube and then thermally extracted at 200C to analyze the volatiles present in various GC septa. For this study we analyzed about 10 different septa from various manufacturers. The results of the analysis of 3 typical GC septa are shown in Figure # 2. The worse septa that we discovered were the HP gray septa. The Supelco Thermogreen LB-2 septa were determined to be the best GC septa on the market. They produced the lowest septa bleed. Only three minor peaks were present which corresponded to the siloxanes listed below. The Restek Green septa (not shown) were almost as good as the Supelco Thermogreen septa. (Table I)
The mass spec peaks listed above are commonly seen in normal GC/MS backgrounds. It must be noted that these siloxanes can originate from other sources besides the GC septum. The second most common source is the GC column stationary phases. Non-polar liquid silicone phases such as DB-1 and DB-5 can contribute to these peaks and care must be used not to exceed the upper temperature limits of any GC column. The GC injection port temperature should never exceed the maximum rated temperature of the liquid phase on the capillary column. Also using a deactivated uncoated fused silica guard column will eliminate any siloxanes originating from the capillary column inside the injection port. This will be discussed later.
PTFE coated GC septum are available from many manufacturers. These work quite well, but only for the first injection. After the first injection the problem of silicone background will return. We confirmed this breakdown of the PTFE coated septum in a test study we conducted on headspace vial septum . The results are shown in Figure #3. This study demonstrates the use of PTFE coated Septa on GC headspace vials utilizing the LEAP headspace sampler. The headspace vial was heated to 120 C and 2.0 mL of the headspace gas was injected into the GC injection port via a heated syringe and cryo-focused at the front of the GC column using our GC Cryo-Trap. In the first injection, no siloxane peaks were detected. However after the second and third injections from the same headspace vial, the siloxane peaks increased dramatically in intensity. This occurs due to the fact that as soon as the PTFE surface is pierced, the inside of the headspace vial is exposed to the silicone material in the pierced section of the septum. With subsequent injections, this exposure increases, resulting in increased contamination of the headspace gas by the silicone polymers. The same results can occur in the GC injection port using these PTFE coated GC septum.
Silicone peaks originating from the septum can also result from the incorrect selection of GC syringe needles. The use of 20 point needles will core out plugs of the septa and deposit these small chips of silicone into the injection port liner. These small pieces of silicone are now exposed to the higher temperatures in the bottom of the injection port and will continually bleed the siloxanes into the GC column, thereby raising the GC background. Side port needles are recommended for headspace systems and thermal desorption systems since they minimize the coring of the GC septa. Side port needles can also be used for direct liquid injections but are more difficult to inject through the septum unless predrilled septum are used. Also as mentioned above, longer syringe needles deposit the samples into the center or lower portion of the injection port further away from the septa area. As a result there is less chance of sample condensation in the septa area of the injection port and also less chance of the liquid solvent from the injected sample washing contaminates off the GC septa.
Injection Port Liners
The GC injection port liner can also be a source of background noise, particularly if it is contaminated. If brown deposits are present in the injection port liner when it is removed from the GC injection port, it should be cleaned or replaced. Contaminated injection port liners can cause loss of sensitivity as well as cause peak tailing. Most manufacturers recommend the thorough cleaning of the injection port liners followed by silylation. The silylation solution is available from Pierce Chemical (Part # 83410). However, we prefer to use injection port liners thoroughly cleaned but NOT silylated, so as to avoid contamination or bleed from the silylation chemicals. We just bake out our injection port liners at high temperature (>350C) before use.A variety of types and shapes of injection port liners are available from many manufacturers. The selection of proper liner is based on the injection type (split or splitless) and the users preference. Most GC injection port liners contribute to poor heat transfer to the septum area as well as to the sample itself. These injection port liners are typically constructed of glass (a poor thermal conductor) and either have a 2.0 or 4.0 mm inside diameter. The large inside diameters are necessary to permit the rapid sample volume expansion when liquid samples are injected into the GC injection port. The glass or quartz material is critical so as to minimize sample decomposition. Quartz material is normally used for applications requiring a more inert surface. These standard glass or quartz injection port liners are sufficient for most applications.
For thermal desorption and headspace applications, we have designed a new injection port liner (S.I.S. part # SIPL10) to provide better heat transfer to the septum area of the injection port and also to the syringe needle. A comparison of the standard glass injection port liner with our new glass lined stainless steel injection port liner is shown in Figure # 4. The new injection port liner is constructed from glass lined stainless steel tubing (GLT). It is necked down to an inside diameter of 0.75 mm in the top portion which just allows for the passage of a standard 0.63 mm diameter syringe needle. The bottom portion of this injection port liner has an inside diameter of 1.0 mm. These small inside diameter injection port liners can be used for small volume liquid injections (less than 1.0 ul) but were specifically designed for use with thermal desorption and headspace injectors in which a rapid gas volume expansion does not take place.
The metal outer liner of these new injection port liners permits the better transfer of heat to the interior of the liner itself as well as to the top of the injection port area. This minimizes the temperature gradient that was demonstrated in Figure # 1. In addition the tight fit of the injection port liner to the syringe needle provides for better heat transfer to the syringe needle and thereby improves the delivery of higher boilers into the GC injection port in the headspace and thermal desorption delivery techniques. This tight fitting area also minimizes the exposure of the septum area to the sample path flow during injection, thereby minimizing condensation of sample on the septum and septum area during sample injection. The result of using these new injection port liners for our thermal desorption and headspace applications has been the ability to analyze higher molecular weight compounds with less contamination of the GC injection port.
In all cases we do recommend a septum purge. The purpose of the septum purge is to minimize the delivery of septa volatiles and condensation materials into the GC column. When used with the injection port liners described above, the septum purge eliminates most of the silicones originating from the septum. With the HP split/splitless injector with EPC (Electron Pressure Control) this septum purge is factory set to 3.0 mL/min. With other HP models without EPC, the septum purge can be set between 0.5 and 5.0 mL/min.
Many users insert a quartz wool plug inside the injection port liner. This is normally used to prevent septum particles from falling down into the injection port liner and plugging the front of the capillary column. As noted by SGE in the 'Mass Spec Tips' section of a previous issue of this newsletter (4), by adjusting the position of the quartz wool plug in the injection port liner so that the syringe needle tip is wiped during the injection, the GC peak shape can be improved, as well as reproducibility and linearity without adversely affecting boiling point discrimination.
Injection Port Liner Seals
The standard O ring injection port liner seals used to form the seals between the injection port liner and the metal injection port can be major sources of foreign peaks in the chromatogram. These O rings are normally made of Viton or Silicone rubber which easily bleed at temperatures above 220C. At temperatures above 250C , they rapidly degrade producing major contamination to the GC injection port. This problem can be minimized by using lower injection port temperatures. However the lower temperatures will compound the septum contamination problem discussed above. Some manufacturers have replaced the O ring seal with a graphite sealing ring. These graphite seals operate efficiently at temperatures up to 400C with no bleed. However the graphite material is very porous and susceptible to sample contamination. The graphite also is very fragile and can easily flake small pieces of graphite into the GC injection port. To overcome this problem a new graphitized Vespel® injection port liner seal was designed (SIS Part # HP13) to replace the O Ring seals for the injection port liners. The graphitized Vespel® seals are soft enough to form a good seal, are non porous, will not flake and are usable to temperatures up to 400C with no bleed into the GC injection port. They also can be reused many times.Cleaning the GC Injection Port
The GC injection port should be cleaned on a regular basis or when it becomes contaminated. The recommended procedures for doing this have been described in previous publications (2, 3), but basically involve the physical cleaning of the injection port with small wire brushes and solvents followed by the baking out of the GC injection port at high temperature with preheated carrier gas and no column installed. The method is outlined in Table II.This high temperature flow conditioning of the GC injection port purges all parts of the injection port with gas at the highest temperature possible. The hot gas flushes the injection port area including the septum area and also flushes the septum purge and split vent lines. Areas of the injection port that are not normally cleaned are thoroughly cleaned and purged during this high temperature flow conditioning.
Figure #5 compares the GC backgrounds before and after cleaning the GC injection port as described above. The chromatograms were obtained by heating the GC injection port to 250C, cryo-trapping the volatiles eluted from the injection port on our GC Cryo-Trap for 5 minutes and then analyzing the trapped volatiles by GC/MS. The background noise present in the injection port before cleaning consisted of a wide variety of compounds including septa bleed and injection port contamination from previous samples injected. After cleaning, only three small peaks corresponding to the 3 siloxanes originating from either the GC septa or the silicone liquid column phase were detected.
GC Capillary Columns
The manufacturers of GC capillary columns are continuing to produce columns with lower and lower column bleed. Since the introduction of bonded phase capillary columns, column bleed has been steadily reduced by the manufacturers. Several years ago J&W introduced the DB5-MS low polarity column specifically designed for mass spectrometer use. It has much lower background originating from column bleed, especially at the higher temperatures, thus permitting the analysis of lower levels of analytes. Recently J&W also introduced a new mid range polarity low bleed column for mass spec use called the DB-35MS to further expand the range of these low bleed columns available. At Pitt Con this year they introduced an even lower bleed DB5 column for mass spec use called the DB-XLB column. This new non-polar capillary column provides for the lowest column bleed. It is therefore highly recommended for all GC/MS analysis where a non-polar capillary column can be used. The comparison in column bleeds for these new low bleed DB5 columns is shown in Figure # 6.
The type and size of capillary column used can also effect the background levels as well as the peak width and sensitivity of the system. The lower the column phase thickness, the lower the column bleed. Therefore whenever practical, thin liquid phases should be used. However as the phase thickness decreases, so does the dynamic capacity of the column. For most applications we recommend a phase thickness of 0.25 microns. Also as the diameter of the capillary column decreases, the sensitivity of the system increases. This is due to the fact that as the diameter decreases, the band width of the peak decreases. Narrower peak widths result in higher peak heights and therefore greater signal-to noise ratios for the same size sample. However, again as the diameter of the column decreases so does the capacity of the column. The standard capillary columns are either 0.25mm or 0.32mm for most applications.
In order to minimize GC background, all columns must be treated with care. Columns should always be operated at the lowest temperature needed to complete the analysis. There is no need to bake out the GC column at 340C every time when only volatile and semi-volatile compounds are being analyzed. When the columns are first installed in the GC oven, they should be temperature and flow conditioned as per the manufacturers recommendation to prepare them for sample analysis. GC capillary columns should never be heated to high temperature without flow through the column. During this conditioning phase, the column should not be hooked up to the mass spec. This will only contaminate the MS source.
Carrier gases used for the GC/MS system should be of the highest purity possible. Hydrocarbon, water and oxygen traps should be used just prior to the carrier gas entering the GC. The use of clean gas with proper filters can drastically lower the chromatogram background and therefore increase the sensitivity of the system. This is shown in Figure # 7. Oxygen is particularly detrimental to the life of the polar DB-WAX or Carbowax columns but should be minimized or eliminated from entering all columns in order to preserve their life. It is very important to eliminate the exposure of capillary columns to oxygen at high temperatures.
GC Cryo-Trap
The GC Cryo-Trap accessory can also increase the signal-to-noise ratios especially for lower boiling analytes when using thermal desorption and headspace GC injection techniques. Due to the cryo-focusing capabilities of this technique, the peak widths of the more volatile analytes are narrowed during the sample injection and cryo-trapping step. As a result of the narrow peak widths, the peak heights are increased, resulting in an increase in the signal-to-noise ratios for the analytes. This technique is especially useful with thermal desorption and headspace GC sample introduction techniques. With both of these techniques, large gas volumes (1 to 100 mL) are injected onto the capillary columns. The cryo-focusing unit traps the organic analytes in a narrow band at the front of the GC column. The analytes are later released in a narrow band that results in sharp GC peaks with good signal-to-noise ratios. The technique can be further improved if a deactivated fused silica guard column is used inside the GC Cryo-Trap instead of trapping on the liquid phase columns. Tests have verified the resolution of the early eluting GC peaks is drastically increased when the deactivated fused silica guard columns are used. These guard columns also extend the life of the GC column. In addition the liquid phase coated column is not inserted into the hot GC injection port where decomposition of the liquid phase could easily occur if the injection port is maintained at constant high temperatures.Column Ferrules
For mass spec applications we prefer the graphitized Vespel® ferrules for all GC column connections. However care must be used when working with graphitized Vespel® ferrules, since the graphitized Vespel® ferrules are hard and they can break the capillary columns if too much pressure is applied to them on installation on the columns. Leaks can also be encountered shortly after using these ferrules. In order to prevent these leaks, the GC oven should be ramped up to the normal operating temperature after the new ferrules are installed, then cooled down to room temperature and the GC nuts and ferrules tightened once again. When this is done, leaks do not normally reappear. The ability to form good leak tight seals is critical to assure good GC peak shape and maximize the life of the GC column. Graphite ferrules are preferred by many users, however these ferrules are soft, will easily flake and are somewhat porous. This porous nature may lead to either contamination by analytes or restrict the ability to form good vacuum tight seals. This inability to form good vacuum seals is particularly crucial at the detector end of the GC column. Therefore we recommend the use of graphitized Vespel® ferrules for all GC/MS applications.Conclusion
GC background originates from many areas of the GC including the GC injection port as well as the GC column oven. In the past the GC septa or capillary columns were considered to be the major culprits of GC background and resulting poor signal-to-noise ratios for the analytes. However as described above this GC background can originate in the injection port itself, from transfer lines, seals and cold spots as well as the GC column itself. The GC background can be readily reduced and signal to-noise ratio can be dramatically increased by incorporating one or more of the following improvements into your system (Table III):
Combining these improvements with the MSD improvements described in the last edition of this newsletter will improve the performance of your MSD or other GC/MS systems.
We welcome comments and additional suggestions from all our readers. I am sure that these last two articles are not all inclusive and I probably missed a few points. So we would encourage you to respond with your ideas. Your input will be published in the Mass Spec Tips section of this newsletter.
References
(1) Improving the Sensitivity in the HP 5971 MSD and Other Mass Spectrometers, Part I, ÒThe Mass Spec SourceÓ, Vol XIX, No. 1, February 1995, pp 3-8.(2) Improving Injection-Port Performance in Gas Chromatography, LC/GC, Vol 13, No. 1, January 1995, pp 48-52.
(3) Elimination of ÒMemory PeaksÓ from Thermal Desorption, S.I.S. Technical Bulletin No. 3, January 1994.
(4) Reduction of Peak Tailing, Mass Spec Tips, ÒThe Mass Spec SourceÓ, Vol XVIII, No. 4, July 1994, pp 10-11.
Part I of Increasing Mass Spec Sensitivity
(Part I | Part II - Increasing Mass Spec Sensitivity)