Description
Desorption Tube and Needle Conditioning Oven for Batch Cleaning and Baking Out of Thermal Desorption Tubes and Needles.
This 24 tube conditioning oven is used for batch flow conditioning of both empty and packed Silco Coated SS desorption tubes as well as for the flow conditioning of the desorption tube needles. The system is designed much like the 6 port conditioning oven but contains a much larger heater block with 24 ports for tubes and needles. Four port manifold handles permit the flow conditioning of 4 tubes or needles from one ball rotameter.
Each of the six adjustable flow bubble rotameters has a flow range between 0 and 50 mL/min, one for each of the manifolds with tubes or needles to be conditioned. Each of the flows to the manifolds can be independently controlled via a microneedle valve and the flow turned off to that port when not needed. A single electrically operated solenoid valve (Gas Valve) turns off or on the gas to all the ports via the Gas Switch on the front panel. On the top of the Conditioning Oven six quick disconnects connect to 1/8" flexible nylon tubing to provide gas flow through the manifolds with desorption tubes and needles during conditioning. When the quick disconnect is removed, the gas flow is automatically closed to that port. By providing gas flow from a carrier gas such as high purity helium or nitrogen through the desorption tubes and needles while conditioning, it can be assured that no oxygen enters the Silco Coated desorption tube which could destroy the adsorbent material. Impurities from the inside of the desorption tubes and needles are flushed through. A single 1/8" fitting on the back of the Conditioning System is provided for the attachment of the carrier gas from the source.
Electrical power to the conditioning system oven is provided from a standard 110 volt, 10 amp outlet. An external high temperature reset switch is located on the rear of the Oven so that if temperatures exceed 350 degrees C on the heater block, the external reset will open and heat to the block will cease. This switch can be reset by simply pushing in the button once the block has cooled sufficiently. Two slo-blow fuses are mounted on the rear of the Conditioning System, one for the main power and one for the heater circuit. In addition a three inch fan enclosed on the back side of the Conditioning System provides a steady flow of air through the system to maintain the temperature of the enclosed electronic components to an acceptable level. If the case temperature exceeds 60 degrees C, an internal switch will cut power to the heater circuit.
Also located on the back of the Conditioning System is a cooling rack. After the heated conditioning of the desorption tubes and needles is complete, the desorption tubes and needles are removed from the oven and placed in the cooling rack. As soon as the tubes are touchable ( 5 to 10 minutes), they are immediately capped on both ends with the stainless steel caps with PTFE seals that are available for the desorption tubes.
Warranty - 90 days parts and labor
Specs
Electrical Specifications |
---|
|
Temperature Controller |
|
Gas / Flow Specifications |
|
Weight and Dimensions |
|
Desorption tubes and needles should be cleaned in the Thermal Desorption Conditioning System before each use to prevent cross contamination of samples.
Part No. | OD (in) | ID (in) | Thickness (in) | Cap Seal | Top Seal | Needle Seal | Acc Seals | Quantity In Stock |
Price EA |
Order | |
---|---|---|---|---|---|---|---|---|---|---|---|
781056 | 24 Port Conditioning Oven, 6 rotameters, programmable temperature controller, 6 - 4 port desorption tube manifold handles, 1 - 4 port needle manifold handle with graphite seals | ||||||||||
--- | --- | --- | --- | --- | --- | --- | DISCONTINUED | --- | --- | ||
781057 | 4 Port Manifold Desorption Tube Handle | ||||||||||
--- | --- | --- | --- | --- | --- | --- | DISCONTINUED | --- | --- | ||
781058 | 4 Port Manifold Needle | ||||||||||
--- | --- | --- | --- | --- | --- | --- | DISCONTINUED | --- | --- | ||
781007 | S.S. Desorption Tube Cap with 0.040in hole for conditioning GLT tube | ||||||||||
--- | --- | --- | --- | --- | --- | --- | 77 | $9.95 | |||
781015 | Graphite Top Sealing Washer | ||||||||||
0.21 | 0.06 | 0.06 | No | Yes | No | Yes | 534 | $14.50 | |||
* Call for availability. | |||||||||||
![]() |
Thermal Desorption Conditioning System
The Desorption Tube Conditioning System is used for the flow conditioning of both empty and packed Silco Coated SS desorption tubes as well as for the flow conditioning of the desorption tube needles.
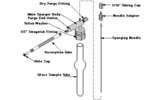
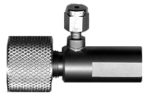
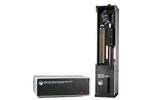
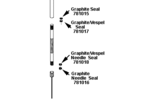
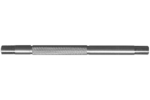
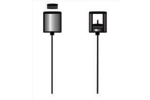
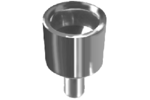
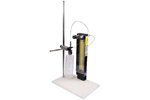
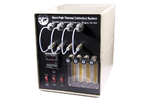
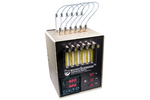